7 Tips To Reduce Lead Time Business Should Know
- Giao Huynh
- Oct 3, 2022
- 3 min read
Lead time is the time elapsed between the start of a process and its completion. Companies consider pre-processing, production processing and finishing, supply chain management and project management lead time steps. By comparing results against established standards, they can identify areas of inefficiency.
Reducing lead time can streamline operations, increase productivity, and increase production and revenue. On the other hand, long lead times negatively affect sales and production.
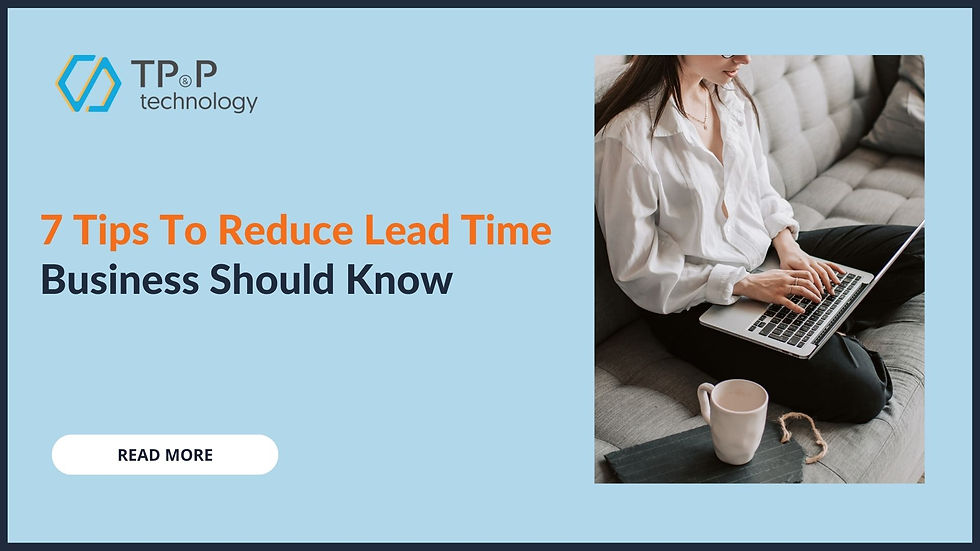
Types of Lead Time
There are three primary types of lead time; each must be considered in conjunction with the others to define the overall expectations of the production process. Therefore, these three basic types generally fall under the fourth type of aggregate lead time.
Customer Lead Time
The customer lead time is the amount of time between when a customer places an order and when the customer receives the product. This includes the time between when a customer places an online order and the company receives the order confirmation. Then, it includes the entire manufacturing process, shipping process, and delivery process.
Material Lead Time
Material lead time is the time from the moment when the company detects the demand for raw materials and the physical acquisition of the material. Companies often receive information about order processing from goods management systems. This lead time can be influenced by information systems that alert management when current inventory levels are low. This can also be affected by procurement, transport, deliveries and delivery by suppliers.
Production Lead Time
After receiving the materials, production time begins. It is the time between when the company has all the resources needed to manufacture the product and when the production process ends. Unlike other lead times, this total lead time must be managed internally and depends on internal factors such as waste, labour, equipment performance, PPE availability and machine downtime.
Cumulative Lead Time
The above delivery times can be combined into a fourth delivery time and companies can track different cumulative delivery times. For example, a company may be interested in an internal lead time (ie when raw materials are purchased after the final product is manufactured).
How to Reduce Lead Time?
While the entire manufacturing and distribution process can be a complex multi-step process, there are steps companies can take to reduce lead times and the number of days in each process. Consider the following ways to reduce your lead time:
Eliminate Unnecessary Processes. The easiest way to reduce turnaround time is to eliminate steps or procedures that are not necessary to facilitate the sale. This may mean forgoing some quality controls or evaluating the efficiency of a production process.
Monitor Transportation Methods. Not all transportation methods are created equally, and some may simply be better options. This relationship is also not static; what may be ideal this month must change due to extenuating circumstances due to labour shortages, natural disasters, or government legislation. A company should always monitor what shipment methods it and its suppliers are using and see if there are preferable methods available.
Incentivize Better Service. Whether external parties such as suppliers or internal parties such as employees, setting incentives, goals/expectations and rewarding those who meet expectations can reduce lead time. Although this creates additional costs for the company, the potential increase in sales volume may outweigh the incentives or bonuses needed to sell the product faster.
Procure Differently. Some providers work faster than others; some suppliers may also be local and require shorter delivery times. In order to reduce lead times, the company should evaluate its current suppliers and see where the benefits can be found.
Carry Higher Inventory. On the other hand, larger inventories increase storage, protection and insurance costs and increase the risk of theft or obsolescence. Alternatively, stock availability means that the company does not have to wait for shipments to arrive.
Reorder More Often. If you don't want larger stocks, you should place material orders more often. This can cause materials to be transported before you know you need them. Although you run the risk of having too much inventory, an alternative is to plan your excess inventory in advance.
Encourage internal learning. An internal production process is only as effective as the people who know it. By prioritizing cross-training and learning opportunities, companies can have a stronger workforce with employees who have more knowledge and skills in the process.
Site-note:
Need Help With Your Software Projects? Contact TP&P Technology - Leading Software Engineering Company in Vietnam Today
Comments